But whether due to a breakdown in communication, inventory listing errors or technological snafus, sometimes buyers wind up with the wrong item. Most studies on picking errors put the rate at between 1% and 3% of all orders. That may not seem like a lot of mistakes, but they add up over time if the rate is consistent from one day, week or month to the next.
With humans being what they are — naturally imperfect — fulfillment foibles will likely never be fully neutralized. But there are a variety of strategies manufacturers can deploy to lower the error rate.
Here are a few tips:
1. Consider a combination of automation solutions
Automation has revolutionized distribution warehouses in a litany of ways, but perhaps the biggest is in terms of minimizing errors. From collaborative mobile robots to pick-to-light technologies, warehouse automation specializes in performing several tasks at once, particularly the labor-intensive ones. Leveraging these and other AI technologies can not only reduce error rates, but make the fulfillment process as a whole much faster. IT also can free up your staff to perform functions that require more thought, deftness or dexterity that a machine cannot adequately replicate.
2. Leverage labels
It may seem obvious, but many order fulfillment problems are resolved with the simplest of solutions. Whether it's through bar code scanners, unique SKUs or tags that are more easily discernible (i.e. bold font, placement, color contrasts, etc.), making sure all items are properly labeled can streamline the picking process for all involved. If the problems with your labeling system aren't readily discernible, picking the brains of your warehouse staff may provide clarity.
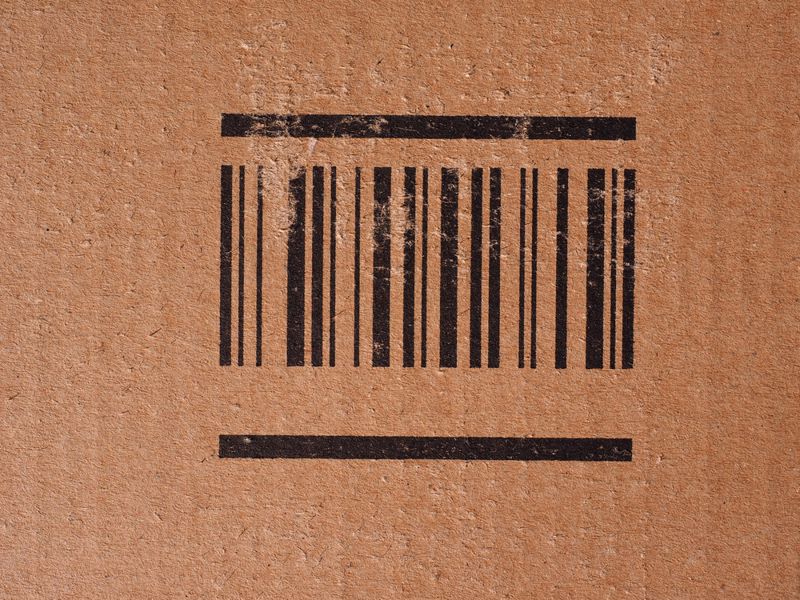
3. Coordinate with other departments
Sometimes, errors in order fulfillment originate with an entirely different department. While the supply chain is increasingly interconnected, fulfillment stands on its own. As a result, if an order goes out that is damaged or defective, the problem may originate with receiving, which didn't recognize the flaw or failed to remove it from the assembly.
This is why it's important to maintain ongoing communication with other departments so problems are recognized before they arrive at fulfillment. Teams may need to flesh out what steps they take to enhance coordination and problem identification.
4. Codify inventory checks
Occasionally, fulfillment errors may stem from problems with inventory, where teams failed to account for items that needed to be replenished due to heavy buyer volume. Crucial to inventory management is consistency. Whether it's carried out once a week, every other week, monthly or some other appropriate interval, inventory management should be very systematic so the steps are easily repeatable and executable. It also ensures that the supply for hot-ticket items that sell quickly aligns with demand.
Post A Comment:
0 comments so far,add yours