Their solution? Instead of sharing and taking up what space was left on container ships, many opted to book their very own.
As chronicled by Supply Chain Dive, several household name corporations chartered bulk vessels as a workaround to the ongoing delays and congestion at major shipping ports. Chartering ships for months at a time is a pricey proposition, fetching upwards of $1 million to $2 million, depending on how long the leases are for. That kind of money is cost-prohibitive for most small and midsize businesses. But for the likes of multinational corporations such as Coca-Cola, The Home Depot, Walmart and other major retailers, it was money well spent by avoiding wasted time.
During an August earnings call, Walmart executives said the company went to these lengths due to stocking issues at several of its locations throughout the country.
"We've chartered vessels ... we've secured capacity for the third and fourth quarter and feel good about the inventory positioning particularly compared to last year with inventory up 20% across the segments," said John Furner, CEO for Walmart U.S.
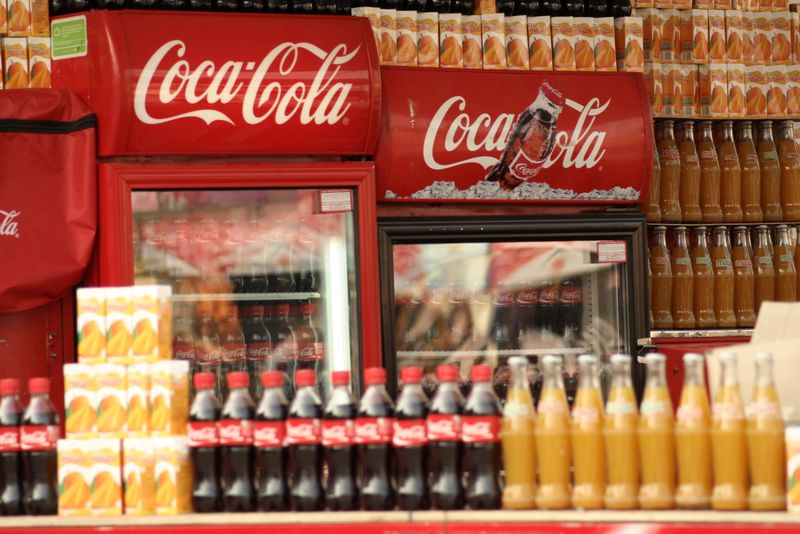
Coca-Cola, Costco and The Home Depot also chartered ships
Another company that chartered its own vessels in 2021 was Coca-Cola. Alan Smith, Coca-Cola's procurement director of global logistics, noted on LinkedIn at the time that the soft drink giant chartered three bulk vessels to haul around 60,000 tons of material.
"[This is a] prime example of excellent collaboration between our procurement teams, our supply chain partners and our suppliers," Smith said, as quoted by Supply Chain Dive.
Home Depot, Costco and Ikea are a few other that chartered container ships at least once in 2021.
Despite ongoing efforts from the federal government and other organizations to clear the bottlenecks, port volume was and remains unrelenting. For instance at the Port of Los Angeles, total volumes in the second quarter of 2020 was 1.03 million TEUs. In 2021 during the same three-month period, it was 1.82 million TEUs. And it can take a number of weeks before vessels can reach port to unload. As of Jan. 4, the wait time was nearly 22 days.
Richard Ungo, director of the Maritime, Ports, and Logistics Institute at Old Dominion University, said such investments can be well worth it for the organizations that have the money to spend. Otherwise, they'd be forced to wait, which ultimately affects the customer and retailers' bottom line.
"Even if they're paying more, they're still not getting the goods on time, Ungo explained. "It makes sense to try to take control of the delivery, and that's why the big companies are taking steps to charter those vessels."